Festo DGST-12-10-PA Käyttöohje
Festo
Ei luokiteltu
DGST-12-10-PA
Lue alta 📖 käyttöohje suomeksi merkille Festo DGST-12-10-PA (3 sivua) kategoriassa Ei luokiteltu. Tämä opas oli hyödyllinen 13 henkilölle ja sai 4.5 tähden keskimäärin 2 käyttäjältä
Sivu 1/3
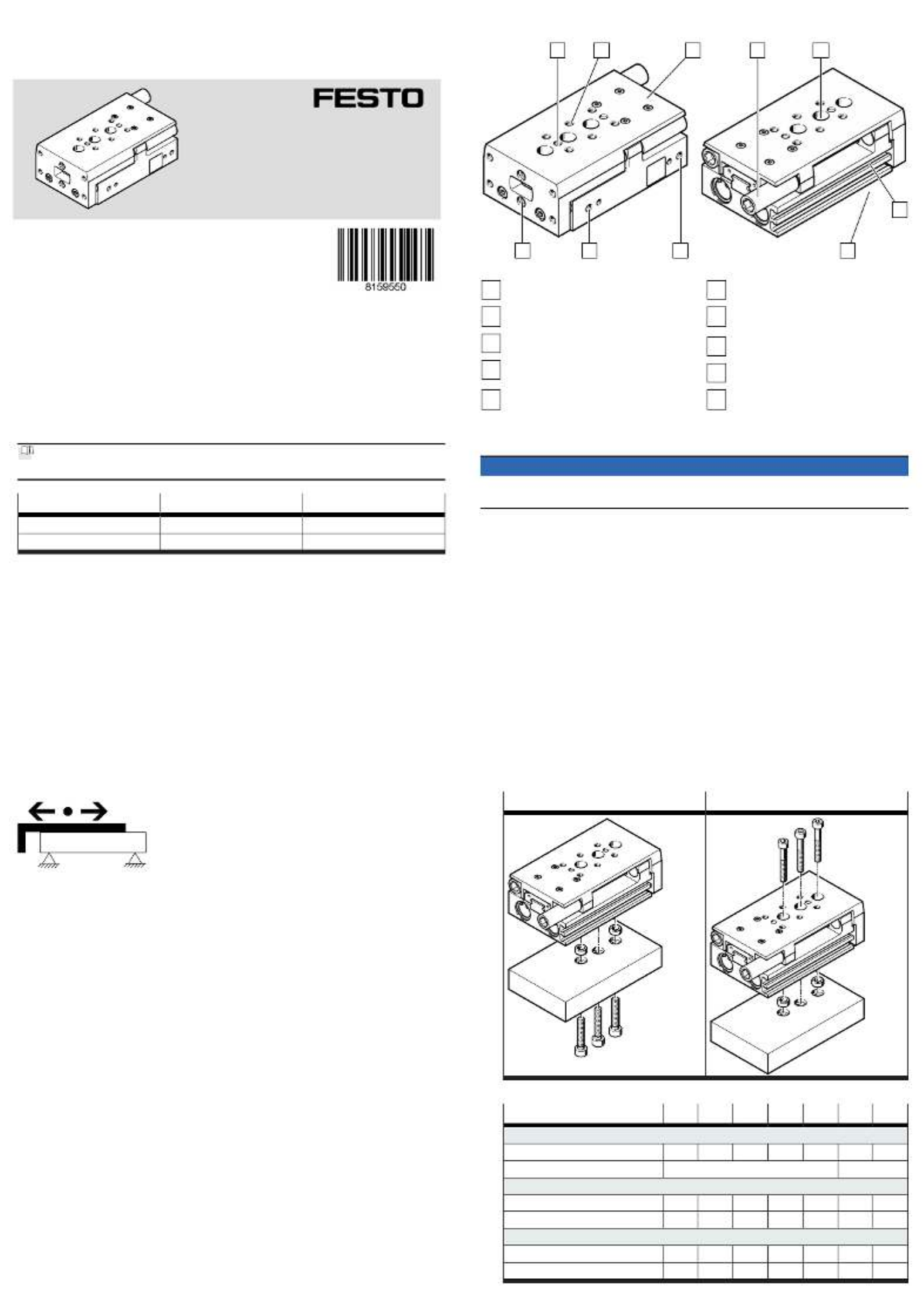
DGST
Mini slide
Festo SE & Co. KG
Ruiter Straße 82
73734 Esslingen
Deutschland
+49 711 347-0
www.festo.com
Operating instructions
8159550
2021-09d
[8159552]
Translation of the original instructions
© 2021 all rights reserved to Festo SE & Co. KG
1 Applicable documents
All available documents for the product
è www.festo.com/sp.
Documents Product Table of contents
Operating instructions Shock absorber DYSS-G8 –
Operating instructions Shock absorber DYEF-G8 –
Tab. 1
2 Safety
2.1 Safety instructions
–Only use the product in its original condition without unauthorised modifica-
tions.
–Take into account the ambient conditions at the location of use.
–Observe the identifications on the product.
–Store the product in a cool, dry environment protected from UV and corrosion.
Keep storage times short.
–Before working on the product, switch off the compressed air supply and lock it
to prevent it from being switched on again.
2.2 Intended use
The product is intended for the space-saving transport of masses. The product is
approved for slide operating mode.
Fig.1
2.3 Training of qualified personnel
Work on the product may only be carried out by qualified personnel who can
evaluate the work and detect dangers. The qualified personnel have skills and
experience in dealing with pneumatic (open-loop) control technology.
3 Additional information
–Contact the regional Festo contact if you have technical problems
è www.festo.com.
–Accessories and spare parts è www.festo.com/catalogue.
4 Function
The product is a non-rotating twin-piston drive with bearing guide.
The slide is moved back and forth by alternate pressurisation of the supply ports.
The slide is braked at the end position by shock absorbers.
5 Product design
1 2 3 4 5
6
78910
Fig.2
1
Centring
2
Thread for mounting the payload
3
Slide
4
Shock absorber with threaded
sleeve
5
Drilled holes for mounting the
mini slide from above
6
Slot for proximity switch
7
Thread for mounting the mini
slide (concealed underneath)
8
Supply port (advance)
9
Supply port (retract)
10
Thread with centring hole for
mounting the payload
6 Transport
NOTICE
Unexpected and unbraked movement of components
• Secure moving components for transport.
1. Take product weight into account
è 11 Technical data.
2. Maintain the support clearance of 300 mm when attaching transportation£
equipment.
7 Assembly
7.1 Preparation
–Position the product to ensure that the operating elements are accessible,
e.g. the clamping components for the shock absorbers.
–Mount the product without torsional stresses.
–Mount the product on a mounting surface with a flatness of 0.05% of the stroke
length, but max. 0.1 mm.
–If necessary: select the mounting components or the accessories. The centring
sleeves are not included in the scope of delivery.
To prevent collisions: mount the mounting components outside the positioning
range.
7.2 Mounting mini slide
1. Mount drive ensuring that the minimum number of screws is used.
Direct fastening Through-hole mounting
2. Tighten screws evenly.
DGST -6 -8 -10 -12 -16 -20 -25
Minimum number of screws dependent on the stroke
10 150 [mm] 2 2 2 2 2 2 2…
200 [mm] – 3
Direct fastening
Screw M4 M4 M5 M5 M6 M8 M8
Centring [H7] [mm] 5 5 7 7 9 12 12
Through-hole mounting
Screw M3 M3 M4 M4 M5 M6 M6
Centring [H7] [mm] 5 5 7 7 9 12 12
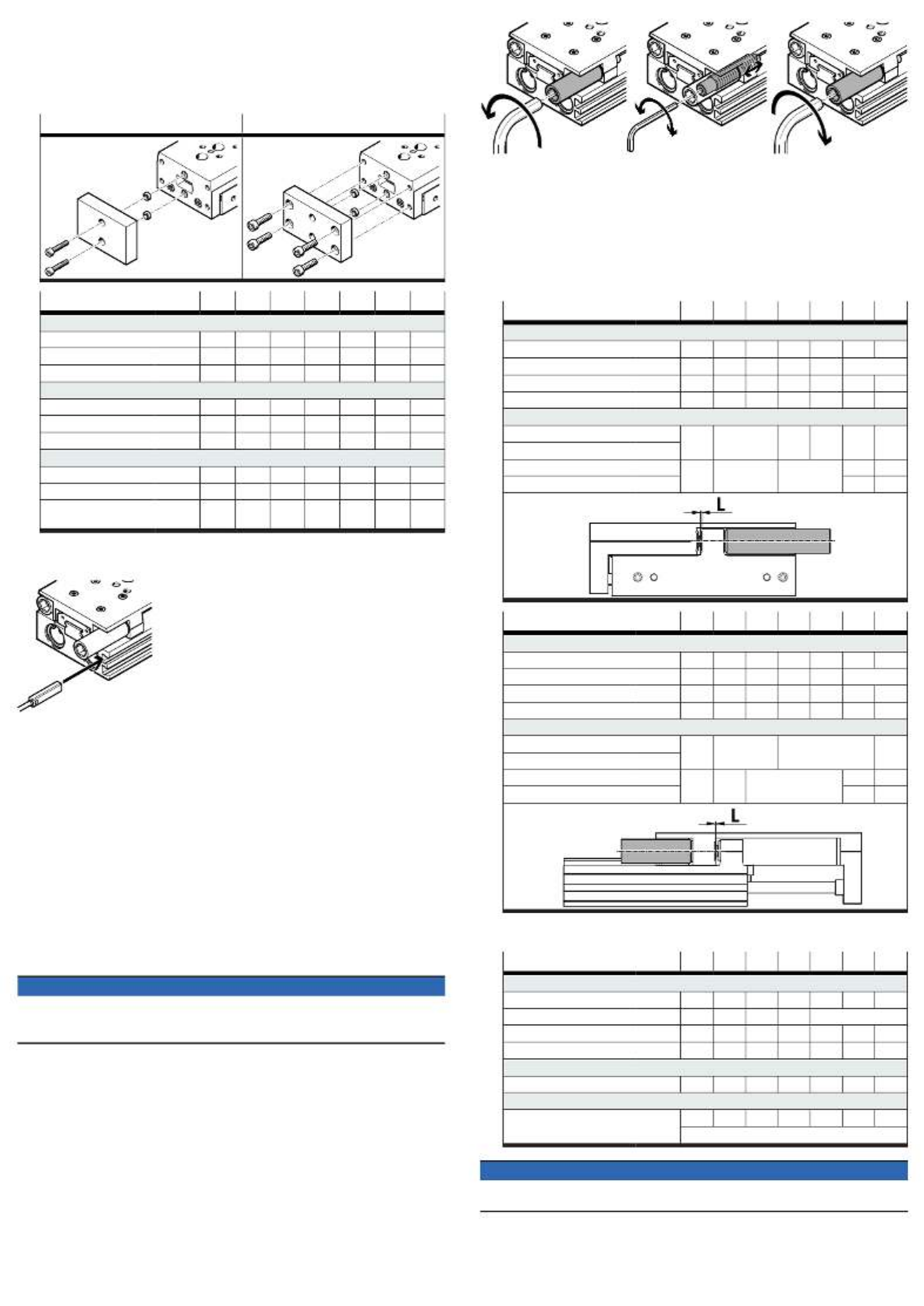
7.3 Mini slide attachment
• Mount the attachment on the slide or the yoke plate with screws and centring
elements. Observe the maximum screw-in depth D.
If necessary: select the mounting components or the accessories
è www.festo.com/catalogue. The centring sleeves are not included in the
scope of delivery.
Mounting with 2 screws Mounting with 4 screws
DGST -6 -8 -10 -12 -16 -20 -25
Mounting on the slide (top)
Screw M3 M3 M4 M4 M5 M5 M6
Max. screw-in depth D [mm] 3.1 5.5 4.5 5.2 7.2 8 11
Centring [H7] [mm] 5 5 5 5 5 12 12ÆÆÆÆÆÆÆ
Mounting on the slide with 2 screws (front)
Screw – M3 M3 M4 M4 M5 M6
Max. screw-in depth D [mm] – 4.7 5.2 6.4 6.4 7.4 7.4
Centring [H7] [mm] – 5 5 7 7 12 12Æ Æ Æ Æ Æ Æ
Mounting on the slide with 4 screws (front)
Screw M3 M3 M4 M4 M5 M5 M6
Max. screw-in depth D [mm] 4.5 4.5 6.5 6.5 8 8 10
Centring [H7] [mm] Æ
2H8
Æ Æ Æ Æ Æ Æ 5 5 7 7 12 12
7.4 Mounting the proximity switches
For position sensing with proximity switches:
Fig. 3: Position sensing
1. Slide the proximity switches into the slots
è Fig. 3.
2. Avoid external influence caused by magnetic or ferritic parts in the vicinity of
the proximity switches. Check the required clearance for the specific applica-
tion.
3. To prevent contamination: use slot covers on all unused slots
è www.festo.com/catalogue.
7.5 Mounting one-way flow control valves
To set the velocity:
• Use one-way flow control valves in the supply ports. They are screwed directly
into the supply ports.
To secure the payload from dropping if the pressure fails:
• Use check valves.
8 Commissioning
8.1 Preparation
NOTICE
Unexpected movement of components.
• Keep foreign objects out of the positioning range.
• Initiate start-up at low speed.
• Slowly pressurise the complete system. Use the on-off valve HEL for slow
start-up pressurisation.
With medium or large payloads or at high speeds:
• Use the sufficiently dimensioned arrester fixtures.
Without the use of external arrester fixtures, the product will withstand the
maximum speeds and payloads defined in the catalogue or the technical
data.
8.2 Adjustment of slide end positions
In the factory settings for the mini slide DGST-...-P/-Y12 the minimum distance L
of the shock absorbers specified below for the slide end positions must be
observed.
Fig. 4: Adjustment of the slide end positions
1. Loosen the threaded sleeves.
2. Position the slides one after the other at the retracted and advanced end
positions.
3. At the end position: screw in the shock absorber to the end position. Do not
exceed the maximum torque when screwing the internal hexagon socket/slot.
Maintain the minimum distance L. If the minimum distance L is not long
enough, the shock absorbers will not be completely effective and the product
will impact internally. This can lead to the destruction of the product.
DGST -6 -8 -10 -12 -16 -20 -25
Shock absorber
DYEF-G8-M...-Y1 4 5 6 8 10 12 14
DYEF-G8-M...-Y1F 4 5 6 8 10 –
DYEF-G8-S-M... 4 5 6 8 10 12 14
DYSS-G8-... 2 3 4 5 7 8 10
Minimum distance L of the mini slide at retracted end position
DGST-...-E-... [mm] 2.1 0.8 0.5 0.7 0.8 1
DGST-...-P-... [mm]
DGST-...-P1-... [mm] 3.1 2.7 2.6 – –
DGST-...-Y12-... [mm] 2.9 3.1
DGST -6 -8 -10 -12 -16 -20 -25
Shock absorber
DYEF-G8-M...-Y1 4 5 6 8 10 12 14
DYEF-G8-M...-Y1F 4 5 6 8 10 –
DYEF-G8-S-M... 4 5 6 8 10 12 14
DYSS-G8-... 2 3 4 5 7 8 10
Minimum distance L of the mini slides at extended end position
DGST-...-E-... [mm] 1.05 1.1 1 1.2
DGST-...-P-... [mm]
DGST-...-P1-... [mm] 1.55 1.5 1.6 – –
DGST-...-Y12-... [mm] 1.5 1.7
4. At the end position: pressurise the slide as a counterhold to the shock
absorber. Tighten the threaded sleeve to the specified tightening torque.
DGST -6 -8 -10 -12 -16 -20 -25
Shock absorber
DYEF-G8-M...-Y1 4 5 6 8 10 12 14
DYEF-G8-M...-Y1F 5 5 6 8 10
DYEF-G8-S-M... 4 5 6 8 10 12 14
DYSS-G8-... 2 3 4 5 7 8 10
Internal hexagon/slot on the shock absorber
Max. torque [Nm] 0.1 0.5 0.6 1 3 5 10
Threaded sleeve
Tightening torque [Nm] 0.4 0.64 0.8 1.6 2.4 4 6.4
Tolerance ± 20%
NOTICE
The exact slide position must be checked during a test run with compressed air
applied and, if necessary, corrected.
1. When operating the DGST-...-E1: restrict the speed.
2. Observe the permissible impact energies è 11 Technical data.
3. Suitable shock absorbers can retrofitted to the product
è www.festo.com/catalogue.
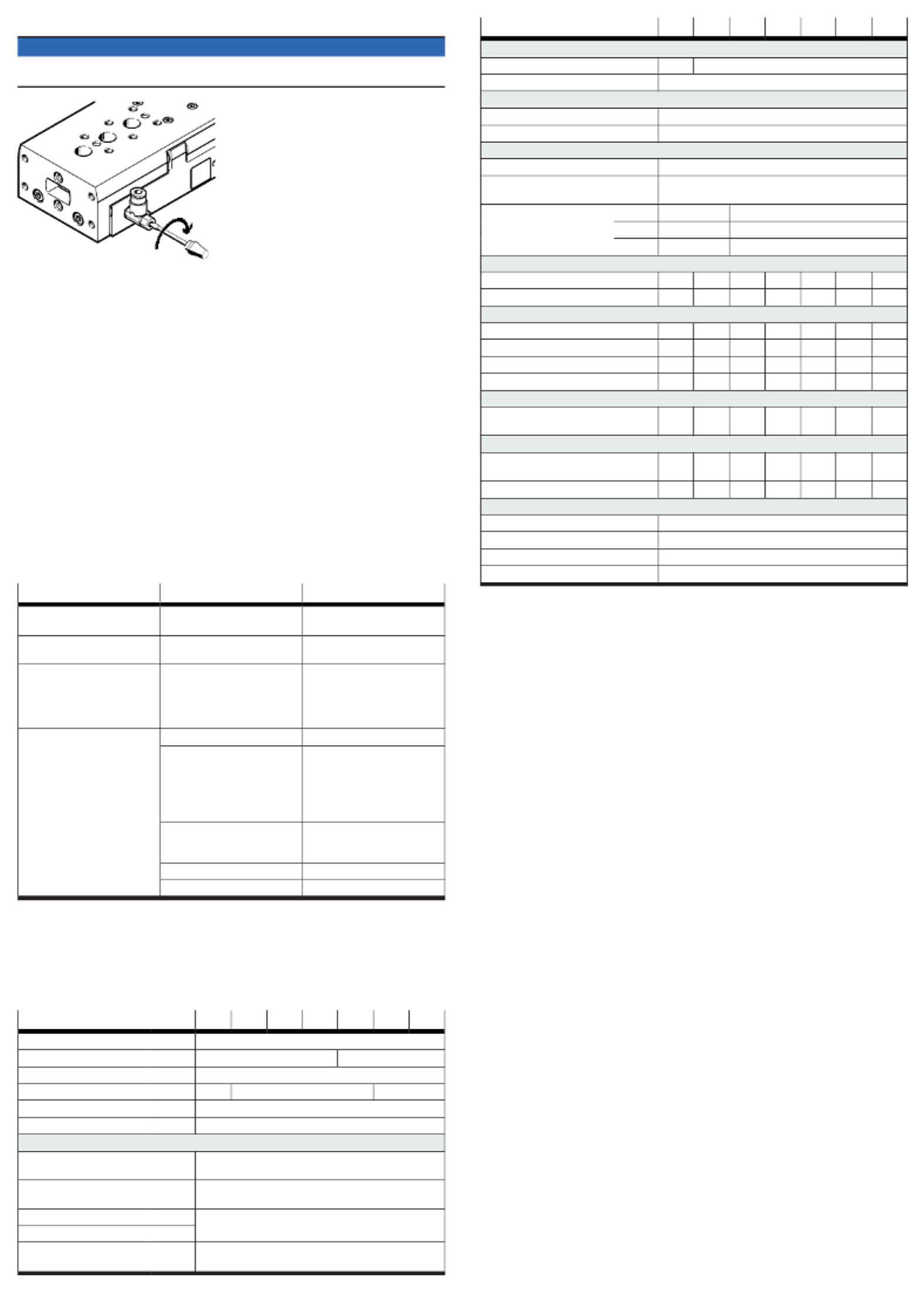
8.3 Test run
NOTICE
Risk of collision by payloads that protrude through the rotor/slide.
• Only turn adjusting screws while the rotor/slide is stationary.
Fig.5
1. Fully close the one-way flow control valves on both sides, then open them one
complete revolution.
2. Pressurise the drive on both sides simultaneously.
ÄThe slide moves slightly to a point of balance.
3. Then exhaust the drive on one side.
ÄThe slide moves to an end position.
4. Start the test run.
5. If needed: correct speed at the one-way flow control valves. The slide should
reach the end positions without striking them harshly or recoiling.
9 Cleaning
Clean the product with a clean, soft cloth and non-abrasive cleaning agents.
For use with reduced particle emission:
–Remove abraded particles and soil from the product:
–Prior to initial commissioning
–Regularly during operation
10 Malfunctions
10.1 Fault clearance
Fault description Cause Remedy
The slide moves unevenly. The one-way flow control valves
are not installed correctly.
Control the exhaust air flow.
The slide is in initial position
despite pressurisation.
The tubing is faulty. Check the tubing.
The slide speed is too low. The air volume is insufficient. –Increase the connection
cross-sections.
–Check the flow control valve
setting.
–Connect a volume upstream.
The slide stops in the end posi-
tion without cushioning.
The speed is too high. Reduce the speed.
The cushioning is too low. –Re-adjust the shock
absorber and the (fixed)
stop è 8.1 Preparation.
–Reduce the speed.
–Check the shock absorbers
and replace if necessary.
The air cushion is not present. Pressurise both supply ports
simultaneously, then exhaust
one side.
The shock absorbers are faulty. Replace the shock absorbers.
The payload is too large Reduce the payload.
Tab. 2: Fault clearance
10.2 Repair
Send the product to the Festo repair service for repair.
–Replacement of shock absorbers è 1 Applicable documents.
11 Technical data
DGST -6 -8 -10 -12 -16 -20 -25
Design Drive with scotch yoke system
Guide Recirculating ball bearing guide Cage guide
Mode of operation double-acting
Pneumatic connection M3 M5 G1/8
Mounting position any
Ambient temperature [°C] –10 … +60
Cushioning
DGST-...-E1 Basic variant with internal, elastic cushioning without
end position adjustment
DGST-...-E Cushioning by external elastic shock absorbers DYEF with
end-position adjustment
DGST-...-P Cushioning by external elastic shock absorbers DYEF-G8
with end-position adjustment
DGST-...-P1
DGST-...-Y12 Cushioning by external hydraulic shock absorbers DYSS-
G8 with end-position adjustment
DGST -6 -8 -10 -12 -16 -20 -25
Max. velocity
DGST-...-E/-P [m/s] 0.5 0.8
DGST-...-E1/-P1/-Y12 [m/s] 0.5
Repetition accuracy
DGST-...-E/-P/-E1 [mm] 0.3£
DGST-...-P1/-Y12 [mm] 0.02£
Operating conditions
Operating medium Compressed air to ISO 8573-1:2010 [7:4:4]
Information on the operating
medium
lubricated operation possible, in which case lubricated
operation will always be required
Operating pressure1) [MPa] 0.15 … 0.8 0.1 … 0.8
[bar] 1.5 … 8 1 … 8
[psi] 22 … 116 15 … 116
Theoretical force
at 6 bar (advancing) [N] 34 60 94 136 241 377 589
at 6 bar (return) [N] 25 45 79 102 207 317 495
Impact energy in the end positions
DGST-...-E/-P [J] 0.018 0.05 0.08 0.12 0.25 0.35 0.45
DGST-...-E1 [J] 0.012 0.03 0.05 0.07 0.15 0.2 0.3
DGST-...-P1 [J] 0.005 0.02 0.03 0.04 0.06 – –
DGST-...-Y12 (per stroke) [J] 0.09 0.18 0.28 0.48 0.85 1.9 3.6
Max. operating frequency
DGST-...-Y12 [cycles/
min]
50 80 80 80 70 50 50
Product weight
DGST-...-E1 with 10 mm
stroke
[g] 90 129 247 391 454 978 1463
DGST-...-E1 at max. stroke [g] 172 310 561 988 1402 3275 4803
Materials
Slide, housing Anodised wrought aluminium alloy
Piston rod high-alloy stainless steel
Guide high-alloy steel, POM, TPE
Seals HNBR/PU
1) With DGST-6/-8/-10/-12 the minimum operating pressure may increase slightly after downtime of 24 h.>
Tab. 3: Technical data DGST
Tuotetiedot
Merkki: | Festo |
Kategoria: | Ei luokiteltu |
Malli: | DGST-12-10-PA |
Tarvitsetko apua?
Jos tarvitset apua merkille Festo DGST-12-10-PA esitä kysymys alla ja muut käyttäjät vastaavat sinulle
Ei luokiteltu Festo Käyttöohjeet

30 Maaliskuuta 2025

30 Maaliskuuta 2025

30 Maaliskuuta 2025

30 Maaliskuuta 2025

30 Maaliskuuta 2025

30 Maaliskuuta 2025

30 Maaliskuuta 2025

30 Maaliskuuta 2025

30 Maaliskuuta 2025

30 Maaliskuuta 2025
Ei luokiteltu Käyttöohjeet
- Ei luokiteltu MSW
- Ei luokiteltu Stamos
- Ei luokiteltu Teka
- Ei luokiteltu Ulsonix
- Ei luokiteltu Aiwa
- Ei luokiteltu Maytag
- Ei luokiteltu Stamony
- Ei luokiteltu Laica
- Ei luokiteltu Thomson
- Ei luokiteltu Amana
- Ei luokiteltu Uniprodo
- Ei luokiteltu Miele
- Ei luokiteltu Whirlpool
- Ei luokiteltu ORNO
- Ei luokiteltu Ledlenser
- Ei luokiteltu Fujifilm
- Ei luokiteltu Etna
- Ei luokiteltu Haier
- Ei luokiteltu KitchenAid
- Ei luokiteltu Bauhn
- Ei luokiteltu Insignia
- Ei luokiteltu Royal Catering
- Ei luokiteltu LG
- Ei luokiteltu Bosch
- Ei luokiteltu Jocel
- Ei luokiteltu Power Dynamics
- Ei luokiteltu BEKO
- Ei luokiteltu Exquisit
- Ei luokiteltu Grundig
- Ei luokiteltu Hisense
- Ei luokiteltu Sharp
- Ei luokiteltu D-Link
- Ei luokiteltu Boneco
- Ei luokiteltu Electrolux
- Ei luokiteltu Apc
- Ei luokiteltu Severin
- Ei luokiteltu Café
- Ei luokiteltu Balay
- Ei luokiteltu DeWalt
- Ei luokiteltu Siemens
- Ei luokiteltu Hama
- Ei luokiteltu Petsafe
- Ei luokiteltu Vorago
- Ei luokiteltu Neewer
- Ei luokiteltu Jensen
- Ei luokiteltu Danby
- Ei luokiteltu Bartscher
- Ei luokiteltu Hartke
- Ei luokiteltu Gigabyte
- Ei luokiteltu Smeg
- Ei luokiteltu Gree
- Ei luokiteltu Hoover
- Ei luokiteltu EBERLE
- Ei luokiteltu Hazet
- Ei luokiteltu Fluke
- Ei luokiteltu Philips
- Ei luokiteltu Goobay
- Ei luokiteltu Topeak
- Ei luokiteltu Antari
- Ei luokiteltu Thermex
- Ei luokiteltu TCL
- Ei luokiteltu Russell Hobbs
- Ei luokiteltu Panduit
- Ei luokiteltu IFM
- Ei luokiteltu Avantree
- Ei luokiteltu Hotpoint
- Ei luokiteltu Schwaiger
- Ei luokiteltu Nabo
- Ei luokiteltu Arendo
- Ei luokiteltu Godox
- Ei luokiteltu Megger
- Ei luokiteltu Balam Rush
- Ei luokiteltu Noxon
- Ei luokiteltu Amica
- Ei luokiteltu Sanus
- Ei luokiteltu Adidas
- Ei luokiteltu Domo
- Ei luokiteltu IKEA
- Ei luokiteltu Cayin
- Ei luokiteltu AEG
- Ei luokiteltu Reflexion
- Ei luokiteltu TP Link
- Ei luokiteltu Inventum
- Ei luokiteltu Totolink
- Ei luokiteltu Shokz
- Ei luokiteltu Gamma
- Ei luokiteltu Medel
- Ei luokiteltu Meris
- Ei luokiteltu Navitel
- Ei luokiteltu Meridian
- Ei luokiteltu Cecotec
- Ei luokiteltu AeroCool
- Ei luokiteltu Kugoo
- Ei luokiteltu Rikon
- Ei luokiteltu Samsung
- Ei luokiteltu Neff
- Ei luokiteltu Garmin
- Ei luokiteltu Razer
- Ei luokiteltu Teufel
- Ei luokiteltu Enermax
- Ei luokiteltu Noveen
- Ei luokiteltu Fender
- Ei luokiteltu StarTech.com
- Ei luokiteltu Origin Storage
- Ei luokiteltu Outwell
- Ei luokiteltu Best
- Ei luokiteltu Stihl
- Ei luokiteltu Delonghi
- Ei luokiteltu Kostal
- Ei luokiteltu ZOTAC
- Ei luokiteltu Comfee
- Ei luokiteltu Imarflex
- Ei luokiteltu Edgestar
- Ei luokiteltu Audient
- Ei luokiteltu Kogan
- Ei luokiteltu Solis
- Ei luokiteltu DJI
- Ei luokiteltu Snom
- Ei luokiteltu McIntosh
- Ei luokiteltu One For All
- Ei luokiteltu Caple
- Ei luokiteltu SereneLife
- Ei luokiteltu Turbosound
- Ei luokiteltu Behringer
- Ei luokiteltu Roesle
- Ei luokiteltu APSystems
- Ei luokiteltu Sony
- Ei luokiteltu GoGEN
- Ei luokiteltu Nitecore
- Ei luokiteltu Create
- Ei luokiteltu Furrion
- Ei luokiteltu Oreg
- Ei luokiteltu Glorious
- Ei luokiteltu Pro-Ject
- Ei luokiteltu Yamaha
- Ei luokiteltu CaviLock
- Ei luokiteltu OOONO
- Ei luokiteltu Xiaomi
- Ei luokiteltu Venom
- Ei luokiteltu Morel
- Ei luokiteltu Kichler
- Ei luokiteltu Topex
- Ei luokiteltu SMART Technologies
- Ei luokiteltu Trust
- Ei luokiteltu Neo
- Ei luokiteltu Morphy Richards
- Ei luokiteltu Newstar
- Ei luokiteltu Legrand
- Ei luokiteltu Integral LED
- Ei luokiteltu Goodram
- Ei luokiteltu Goldtouch
- Ei luokiteltu Lutec
- Ei luokiteltu Vello
- Ei luokiteltu Asus
- Ei luokiteltu Cudy
- Ei luokiteltu Midea
- Ei luokiteltu SBS
- Ei luokiteltu Hayter
- Ei luokiteltu BlueBuilt
- Ei luokiteltu Eufy
- Ei luokiteltu Gys
- Ei luokiteltu Conair
- Ei luokiteltu Franke
- Ei luokiteltu Husqvarna
- Ei luokiteltu Sauber
- Ei luokiteltu Candy
- Ei luokiteltu Shimano
- Ei luokiteltu Axis
- Ei luokiteltu Tamron
- Ei luokiteltu Liebherr
- Ei luokiteltu Carson
- Ei luokiteltu Gourmetmaxx
- Ei luokiteltu Viking
- Ei luokiteltu Gembird
- Ei luokiteltu Truelife
- Ei luokiteltu AkYtec
- Ei luokiteltu Busch-Jaeger
- Ei luokiteltu ETA
- Ei luokiteltu Voltcraft
- Ei luokiteltu Axor
- Ei luokiteltu Duravit
- Ei luokiteltu Karran
- Ei luokiteltu Elkay
- Ei luokiteltu Brennenstuhl
- Ei luokiteltu Extron
- Ei luokiteltu My Wall
- Ei luokiteltu Lindy
- Ei luokiteltu HP
- Ei luokiteltu HiLook
- Ei luokiteltu Aputure
- Ei luokiteltu Netgear
- Ei luokiteltu BaByliss
- Ei luokiteltu Honor
- Ei luokiteltu XP-PEN
- Ei luokiteltu Danfoss
- Ei luokiteltu Riccar
- Ei luokiteltu Orbegozo
- Ei luokiteltu Media-tech
- Ei luokiteltu Kuppersbusch
- Ei luokiteltu BOYA
- Ei luokiteltu Mebby
- Ei luokiteltu Pioneer
- Ei luokiteltu NEO Tools
- Ei luokiteltu TONI&GUY
- Ei luokiteltu Gorenje
- Ei luokiteltu Summit
- Ei luokiteltu Accucold
- Ei luokiteltu EarFun
- Ei luokiteltu Toolcraft
- Ei luokiteltu Gram
- Ei luokiteltu WarmlyYours
- Ei luokiteltu Gemini
- Ei luokiteltu Somfy
- Ei luokiteltu Lorex
- Ei luokiteltu Catit
- Ei luokiteltu NuPrime
- Ei luokiteltu Ecler
- Ei luokiteltu Roccat
- Ei luokiteltu AudioControl
- Ei luokiteltu Elsner
- Ei luokiteltu Kask
- Ei luokiteltu Digitus
- Ei luokiteltu Stokke
- Ei luokiteltu Cabasse
- Ei luokiteltu Koenic
- Ei luokiteltu Panasonic
- Ei luokiteltu Beaphar
- Ei luokiteltu Sure Petcare
- Ei luokiteltu Rotel
- Ei luokiteltu Livall
- Ei luokiteltu KEF
- Ei luokiteltu Monogram
- Ei luokiteltu Sortimo
- Ei luokiteltu Unicol
- Ei luokiteltu Audio-Technica
- Ei luokiteltu Olimpia Splendid
- Ei luokiteltu Lian Li
- Ei luokiteltu JLab
- Ei luokiteltu Toa
- Ei luokiteltu Marantz
- Ei luokiteltu Knog
- Ei luokiteltu Rega
- Ei luokiteltu Vox
- Ei luokiteltu Mars Gaming
- Ei luokiteltu Kerbl
- Ei luokiteltu Metra
- Ei luokiteltu Pyle
- Ei luokiteltu Westinghouse
- Ei luokiteltu Sencor
- Ei luokiteltu Cello
- Ei luokiteltu Hobby
- Ei luokiteltu Lenovo
- Ei luokiteltu Medion
- Ei luokiteltu Noctua
- Ei luokiteltu Klein Tools
- Ei luokiteltu LevelOne
- Ei luokiteltu Shure
- Ei luokiteltu Michael Todd Beauty
- Ei luokiteltu GRAUGEAR
- Ei luokiteltu Trixie
- Ei luokiteltu Schneider
- Ei luokiteltu Lorelli
- Ei luokiteltu Roland
- Ei luokiteltu OBSBOT
- Ei luokiteltu Epson
- Ei luokiteltu SuperTooth
- Ei luokiteltu Kluge
- Ei luokiteltu Bobrick
- Ei luokiteltu Signature Hardware
- Ei luokiteltu Martin
- Ei luokiteltu Kanto
- Ei luokiteltu Scott
- Ei luokiteltu Delta
- Ei luokiteltu Kindermann
- Ei luokiteltu Robern
- Ei luokiteltu Hortus
- Ei luokiteltu DeLock
- Ei luokiteltu Bertazzoni
- Ei luokiteltu Coyote
- Ei luokiteltu Kidde
- Ei luokiteltu Anker
- Ei luokiteltu Growatt
- Ei luokiteltu Nanoleaf
- Ei luokiteltu Stirling
- Ei luokiteltu Mistral
- Ei luokiteltu JVC
- Ei luokiteltu VMV
- Ei luokiteltu S.M.S.L
- Ei luokiteltu Privileg
- Ei luokiteltu MPM
- Ei luokiteltu Niceboy
- Ei luokiteltu Engenius
- Ei luokiteltu Khind
- Ei luokiteltu Motorola
- Ei luokiteltu EMOS
- Ei luokiteltu CyberPower
- Ei luokiteltu Sharper Image
- Ei luokiteltu RGBlink
- Ei luokiteltu Clean Air Optima
- Ei luokiteltu Manfrotto
- Ei luokiteltu Cosatto
- Ei luokiteltu Lego
- Ei luokiteltu Fluval
- Ei luokiteltu Cleco
- Ei luokiteltu Kicker
- Ei luokiteltu Bauknecht
- Ei luokiteltu Gude
- Ei luokiteltu Auna
- Ei luokiteltu Taurus
- Ei luokiteltu Heatit
- Ei luokiteltu Midland
- Ei luokiteltu Field Optics
- Ei luokiteltu Zebra
- Ei luokiteltu Yealink
- Ei luokiteltu FIMI
- Ei luokiteltu Optex
- Ei luokiteltu Frigidaire
- Ei luokiteltu Levoit
- Ei luokiteltu Deye
- Ei luokiteltu Dimplex
- Ei luokiteltu OSD Audio
- Ei luokiteltu Nibe
- Ei luokiteltu Ryobi
- Ei luokiteltu Dremel
- Ei luokiteltu Breville
- Ei luokiteltu Kodak
- Ei luokiteltu Velleman
- Ei luokiteltu Sharkoon
- Ei luokiteltu Laserliner
- Ei luokiteltu Segway
- Ei luokiteltu Cameo
- Ei luokiteltu Casio
- Ei luokiteltu DataVideo
- Ei luokiteltu RGV
- Ei luokiteltu Hendi
- Ei luokiteltu Gamdias
- Ei luokiteltu Concept
- Ei luokiteltu BeamZ
- Ei luokiteltu Livoo
- Ei luokiteltu Nexa
- Ei luokiteltu Guzzanti
- Ei luokiteltu XO
- Ei luokiteltu Steinel
- Ei luokiteltu Bluesound
- Ei luokiteltu Flex
- Ei luokiteltu Chauvin Arnoux
- Ei luokiteltu Blackstar
- Ei luokiteltu Caso
- Ei luokiteltu Hertz
- Ei luokiteltu Kenwood
- Ei luokiteltu Cambridge
- Ei luokiteltu Nobo
- Ei luokiteltu Dell
- Ei luokiteltu Ciarra
- Ei luokiteltu Brandson
- Ei luokiteltu Mybeo
- Ei luokiteltu Aplic
- Ei luokiteltu CSL
- Ei luokiteltu Zoom
- Ei luokiteltu Tru Components
- Ei luokiteltu Hitachi
- Ei luokiteltu Fisher Paykel
- Ei luokiteltu Bearware
- Ei luokiteltu Moen
- Ei luokiteltu Fulgor Milano
- Ei luokiteltu Viewsonic
- Ei luokiteltu B-tech
- Ei luokiteltu Hyundai
- Ei luokiteltu IMM Photonics
- Ei luokiteltu Hansgrohe
- Ei luokiteltu Maginon
- Ei luokiteltu Speco Technologies
- Ei luokiteltu Nec
- Ei luokiteltu IFi Audio
- Ei luokiteltu Tripp Lite
- Ei luokiteltu Nevir
- Ei luokiteltu Infiniton
- Ei luokiteltu Sennheiser
- Ei luokiteltu Ag Neovo
- Ei luokiteltu Henry Engineering
- Ei luokiteltu Taco Tuesday
- Ei luokiteltu Wire Technologies
- Ei luokiteltu GPO
- Ei luokiteltu Block
- Ei luokiteltu Maxi-Cosi
- Ei luokiteltu Ufesa
- Ei luokiteltu Milwaukee
- Ei luokiteltu Smart-AVI
- Ei luokiteltu CEEM
- Ei luokiteltu CAME-TV
- Ei luokiteltu A-Designs
- Ei luokiteltu EchoMaster
- Ei luokiteltu Krups
- Ei luokiteltu Crimson
- Ei luokiteltu Elgato
- Ei luokiteltu Corsair
- Ei luokiteltu Generac
- Ei luokiteltu EVE
- Ei luokiteltu Dahua Technology
- Ei luokiteltu Cambium Networks
- Ei luokiteltu Safety 1st
- Ei luokiteltu Scarlett
- Ei luokiteltu Axxess
- Ei luokiteltu Advance
- Ei luokiteltu Indesit
- Ei luokiteltu Daikin
- Ei luokiteltu Shoprider
- Ei luokiteltu Canon
- Ei luokiteltu Rowenta
- Ei luokiteltu VAIS Technology
- Ei luokiteltu Zephyr
- Ei luokiteltu Maxsa
- Ei luokiteltu Kern
- Ei luokiteltu Lincoln Electric
- Ei luokiteltu BRIO
- Ei luokiteltu Taylor
- Ei luokiteltu AXESS
- Ei luokiteltu DAB
- Ei luokiteltu Be Cool
- Ei luokiteltu Bluetti
- Ei luokiteltu Blaupunkt
- Ei luokiteltu Thermaltake
- Ei luokiteltu Artsound
- Ei luokiteltu Simrad
- Ei luokiteltu Volcano
- Ei luokiteltu Nordic Winter
- Ei luokiteltu TechBite
- Ei luokiteltu Master
- Ei luokiteltu NEP
- Ei luokiteltu Catlink
- Ei luokiteltu Cablexpert
- Ei luokiteltu Ansmann
- Ei luokiteltu Røde
- Ei luokiteltu Makita
- Ei luokiteltu Einhell
- Ei luokiteltu Elac
- Ei luokiteltu Lewitt
- Ei luokiteltu Anova
- Ei luokiteltu Posiflex
- Ei luokiteltu Planet
- Ei luokiteltu Biostar
- Ei luokiteltu Mitsubishi
- Ei luokiteltu HeadRush
- Ei luokiteltu Marshall
- Ei luokiteltu Showtec
- Ei luokiteltu PCE
- Ei luokiteltu Hikvision
- Ei luokiteltu Sitecom
- Ei luokiteltu Navman
- Ei luokiteltu JIMMY
- Ei luokiteltu Equip
- Ei luokiteltu Conceptronic
- Ei luokiteltu Sirius
- Ei luokiteltu Noyafa
- Ei luokiteltu Yorkville
- Ei luokiteltu Toro
- Ei luokiteltu Intermatic
- Ei luokiteltu Spear & Jackson
- Ei luokiteltu Tower
- Ei luokiteltu Hubble Connected
- Ei luokiteltu McGregor
- Ei luokiteltu Habitat
- Ei luokiteltu MSR
- Ei luokiteltu Entes
- Ei luokiteltu V-Tac
- Ei luokiteltu Salton
- Ei luokiteltu Novation
- Ei luokiteltu Chipolino
- Ei luokiteltu Alphatronics
- Ei luokiteltu Fezz
- Ei luokiteltu Eden
- Ei luokiteltu Fuxtec
- Ei luokiteltu Graef
- Ei luokiteltu Megasat
- Ei luokiteltu SolaX Power
- Ei luokiteltu Valcom
- Ei luokiteltu Mikrotik
- Ei luokiteltu Yale
- Ei luokiteltu Mosconi
- Ei luokiteltu Kohler
- Ei luokiteltu Envertec
- Ei luokiteltu Celly
- Ei luokiteltu Metabo
- Ei luokiteltu Jabra
- Ei luokiteltu Alphacool
- Ei luokiteltu Belanger
- Ei luokiteltu Cuisinart
- Ei luokiteltu Doepke
- Ei luokiteltu Lupine
- Ei luokiteltu Anton/Bauer
- Ei luokiteltu Acer
- Ei luokiteltu Dometic
- Ei luokiteltu JBL
- Ei luokiteltu Rigol
- Ei luokiteltu Joy-it
- Ei luokiteltu Body Solid
- Ei luokiteltu Infinity
- Ei luokiteltu DeepCool
- Ei luokiteltu Kali Audio
- Ei luokiteltu Chief
- Ei luokiteltu Majority
- Ei luokiteltu Cybex
- Ei luokiteltu Iiyama
- Ei luokiteltu Nedis
- Ei luokiteltu Crock-Pot
- Ei luokiteltu Helix
- Ei luokiteltu Genesis
- Ei luokiteltu Dyson
- Ei luokiteltu SKS
- Ei luokiteltu Elation
- Ei luokiteltu Magmatic
- Ei luokiteltu Supermicro
- Ei luokiteltu Zendure
- Ei luokiteltu Logilink
- Ei luokiteltu Majestic
- Ei luokiteltu Basetech
- Ei luokiteltu Leviton
- Ei luokiteltu Soundstream
- Ei luokiteltu Klipsch
- Ei luokiteltu PAC
- Ei luokiteltu Xaoc
- Ei luokiteltu Eldom
- Ei luokiteltu Fisher And Paykel
- Ei luokiteltu Hohner
- Ei luokiteltu Britax
- Ei luokiteltu Elba
- Ei luokiteltu Steiner
- Ei luokiteltu Vonroc
- Ei luokiteltu Worx
- Ei luokiteltu Brentwood
- Ei luokiteltu Philco
- Ei luokiteltu Bellari
- Ei luokiteltu Gossen Metrawatt
- Ei luokiteltu Rolls
- Ei luokiteltu MSI
- Ei luokiteltu Chauvet
- Ei luokiteltu Ordo
- Ei luokiteltu Ground Zero
- Ei luokiteltu OnePlus
- Ei luokiteltu V7
- Ei luokiteltu Jenn-Air
- Ei luokiteltu CRUX
- Ei luokiteltu Karma
- Ei luokiteltu Ridem
- Ei luokiteltu Glemm
- Ei luokiteltu StarIink
- Ei luokiteltu Prixton
- Ei luokiteltu HomeCraft
- Ei luokiteltu Nostalgia
- Ei luokiteltu GameDay
- Ei luokiteltu X-Lite
- Ei luokiteltu Söll
- Ei luokiteltu Sparkle
- Ei luokiteltu Edouard Rousseau
- Ei luokiteltu Lawn Star
- Ei luokiteltu Caberg
- Ei luokiteltu Exped
- Ei luokiteltu Igloo
- Ei luokiteltu Heusinkveld
- Ei luokiteltu KED
- Ei luokiteltu EPEVER
- Ei luokiteltu Grothe
- Ei luokiteltu Cane Creek
- Ei luokiteltu Swiss Eye
- Ei luokiteltu SilverStone
- Ei luokiteltu Goodis
- Ei luokiteltu Seiko
- Ei luokiteltu TFA
- Ei luokiteltu X Rocker
- Ei luokiteltu Dreame
- Ei luokiteltu Foreo
- Ei luokiteltu Speed-Link
- Ei luokiteltu Tesla
- Ei luokiteltu Aquael
- Ei luokiteltu Renkforce
- Ei luokiteltu Graff
- Ei luokiteltu Klarstein
- Ei luokiteltu Lauten Audio
- Ei luokiteltu Toddy
- Ei luokiteltu Lexivon
- Ei luokiteltu Icy Dock
- Ei luokiteltu Elta
- Ei luokiteltu ASI
- Ei luokiteltu Gurari
- Ei luokiteltu Varia
- Ei luokiteltu SPL
- Ei luokiteltu I-Tec
- Ei luokiteltu Xigmatek
- Ei luokiteltu Storcube
- Ei luokiteltu Tracer
- Ei luokiteltu Shark
- Ei luokiteltu REMKO
- Ei luokiteltu Phanteks
- Ei luokiteltu EnOcean
- Ei luokiteltu EK Water Blocks
- Ei luokiteltu Hoymiles
- Ei luokiteltu Envertech
- Ei luokiteltu Cougar
- Ei luokiteltu Asrock
- Ei luokiteltu Bestron
- Ei luokiteltu Audiotec Fischer
- Ei luokiteltu HMS Premium
- Ei luokiteltu PCE Instruments
- Ei luokiteltu Dedra
- Ei luokiteltu Furman
- Ei luokiteltu Abac
- Ei luokiteltu Cata
- Ei luokiteltu Vivax
- Ei luokiteltu Black Diamond
- Ei luokiteltu Advantech
- Ei luokiteltu Stanley
- Ei luokiteltu QSC
- Ei luokiteltu Bitspower
- Ei luokiteltu Black And Decker
- Ei luokiteltu Weston
- Ei luokiteltu Sauter
- Ei luokiteltu WHD
- Ei luokiteltu Schuberth
- Ei luokiteltu Q Acoustics
- Ei luokiteltu Scotsman
- Ei luokiteltu Plantronics
- Ei luokiteltu Proctor Silex
- Ei luokiteltu Radial Engineering
- Ei luokiteltu Karcher
- Ei luokiteltu Orion
- Ei luokiteltu A-NeuVideo
- Ei luokiteltu Beem
- Ei luokiteltu Atlona
- Ei luokiteltu EZ Dupe
- Ei luokiteltu Becken
- Ei luokiteltu I-PRO
- Ei luokiteltu DVDO
- Ei luokiteltu GoXtreme
- Ei luokiteltu Primacoustic
- Ei luokiteltu Avanti
- Ei luokiteltu Acros
- Ei luokiteltu Phil And Teds
- Ei luokiteltu Jotul
- Ei luokiteltu Thermarest
- Ei luokiteltu Powerplus
- Ei luokiteltu Ozito
- Ei luokiteltu Vivanco
- Ei luokiteltu TC Electronic
- Ei luokiteltu Suzuki
- Ei luokiteltu Bionaire
- Ei luokiteltu Huslog
- Ei luokiteltu Glem Gas
- Ei luokiteltu Apogee
- Ei luokiteltu Atomos
- Ei luokiteltu IOptron
- Ei luokiteltu Palmer
- Ei luokiteltu R-Go Tools
- Ei luokiteltu Drayton
- Ei luokiteltu Spektrum
- Ei luokiteltu Jung
- Ei luokiteltu Götze & Jensen
- Ei luokiteltu Native Instruments
- Ei luokiteltu Homedics
- Ei luokiteltu Xvive
- Ei luokiteltu True
- Ei luokiteltu AMX
- Ei luokiteltu Perlick
- Ei luokiteltu Uniden
- Ei luokiteltu Peavey
- Ei luokiteltu BenQ
- Ei luokiteltu Princess
- Ei luokiteltu FOX ESS
- Ei luokiteltu Waterstone
- Ei luokiteltu Mr Steam
- Ei luokiteltu Crown
- Ei luokiteltu DCS
- Ei luokiteltu Fresh N Rebel
- Ei luokiteltu DuroStar
- Ei luokiteltu Duromax
- Ei luokiteltu Owon
- Ei luokiteltu REVITIVE
- Ei luokiteltu Fosi Audio
- Ei luokiteltu Europalms
- Ei luokiteltu Nikon
- Ei luokiteltu HMD
- Ei luokiteltu Sven
- Ei luokiteltu Global Water
- Ei luokiteltu Hamilton Beach
- Ei luokiteltu Extech
- Ei luokiteltu Gaggia
- Ei luokiteltu Tunturi
- Ei luokiteltu Craftsman
- Ei luokiteltu SAVS
- Ei luokiteltu Hansa
- Ei luokiteltu Gastronoma
- Ei luokiteltu Lumens
- Ei luokiteltu Brizo
- Ei luokiteltu Xinfrared
- Ei luokiteltu Getac
- Ei luokiteltu ProLights
- Ei luokiteltu Phonak
- Ei luokiteltu Cherub
- Ei luokiteltu Luxul
- Ei luokiteltu Aruba
- Ei luokiteltu WiiM
- Ei luokiteltu Thor
- Ei luokiteltu Laurastar
- Ei luokiteltu Ambiano
- Ei luokiteltu Horizon
- Ei luokiteltu Bissell
- Ei luokiteltu Antelope Audio
- Ei luokiteltu ESYLUX
- Ei luokiteltu Austral
- Ei luokiteltu Y-brush
- Ei luokiteltu LiveU
- Ei luokiteltu RF-Links
- Ei luokiteltu Fortinge
- Ei luokiteltu Mercury
- Ei luokiteltu Vaddio
- Ei luokiteltu InFocus
- Ei luokiteltu Stinger
- Ei luokiteltu NEXTO DI
- Ei luokiteltu Abus
- Ei luokiteltu AV Tool
- Ei luokiteltu Adventure Kings
- Ei luokiteltu EQ Acoustics
- Ei luokiteltu Michigan
- Ei luokiteltu Vent-A-Hood
- Ei luokiteltu Audix
- Ei luokiteltu Vizio
- Ei luokiteltu Livarno Lux
- Ei luokiteltu Grillmeister
- Ei luokiteltu Ernesto
- Ei luokiteltu Neno
- Ei luokiteltu Rommelsbacher
- Ei luokiteltu One Control
- Ei luokiteltu Bome
- Ei luokiteltu Redback Technologies
- Ei luokiteltu ESX
- Ei luokiteltu City Theatrical
- Ei luokiteltu Omnitronic
- Ei luokiteltu Reber
- Ei luokiteltu Kaiser Nienhaus
- Ei luokiteltu Crestron
- Ei luokiteltu Eurolite
- Ei luokiteltu Manhattan
- Ei luokiteltu Miniland
- Ei luokiteltu Xavax
- Ei luokiteltu MOZA
- Ei luokiteltu Rocstor
- Ei luokiteltu Eureka
- Ei luokiteltu Cruz
- Ei luokiteltu Newland
- Ei luokiteltu Casalux
- Ei luokiteltu Edimax
- Ei luokiteltu Dragonshock
- Ei luokiteltu Russound
- Ei luokiteltu Adj
- Ei luokiteltu Olivetti
- Ei luokiteltu EVOLVEO
- Ei luokiteltu Stadler Form
- Ei luokiteltu Techno Line
- Ei luokiteltu MEE Audio
- Ei luokiteltu Wolfcraft
- Ei luokiteltu Monacor
- Ei luokiteltu Heinner
- Ei luokiteltu Minolta
- Ei luokiteltu Sena
- Ei luokiteltu Innoliving
- Ei luokiteltu Active Era
- Ei luokiteltu Aqara
- Ei luokiteltu POGS
- Ei luokiteltu Beghelli
- Ei luokiteltu BodyCraft
- Ei luokiteltu Superrollo
- Ei luokiteltu Mx Onda
- Ei luokiteltu Koolatron
- Ei luokiteltu Coca-Cola
- Ei luokiteltu Bixolon
- Ei luokiteltu Maruyama
- Ei luokiteltu Bravilor Bonamat
- Ei luokiteltu Kenmore
- Ei luokiteltu Hilti
- Ei luokiteltu D-Jix
- Ei luokiteltu Black Hydra
- Ei luokiteltu I.safe Mobile
- Ei luokiteltu Electro-Voice
- Ei luokiteltu Nimbus
- Ei luokiteltu Lowrance
- Ei luokiteltu Proscan
- Ei luokiteltu Roxio
- Ei luokiteltu Meireles
- Ei luokiteltu Accsoon
- Ei luokiteltu Inspire
- Ei luokiteltu Sebo
- Ei luokiteltu Wharfedale
- Ei luokiteltu Boss
- Ei luokiteltu Tannoy
- Ei luokiteltu Prompter People
- Ei luokiteltu Teltonika
- Ei luokiteltu JL Audio
- Ei luokiteltu Edesa
- Ei luokiteltu IOIO
- Ei luokiteltu Genexis
- Ei luokiteltu Buzz Rack
- Ei luokiteltu ZKTeco
- Ei luokiteltu Giordani
- Ei luokiteltu Cadel
- Ei luokiteltu Dualit
- Ei luokiteltu Atlas Sound
- Ei luokiteltu Solo
- Ei luokiteltu Realme
- Ei luokiteltu Wagner
- Ei luokiteltu Ariete
- Ei luokiteltu Bluestork
- Ei luokiteltu Davis
- Ei luokiteltu Comica
- Ei luokiteltu AddLiving
- Ei luokiteltu Melitta
- Ei luokiteltu Constructa
- Ei luokiteltu Lowell
- Ei luokiteltu INOGENI
- Ei luokiteltu Nearity
- Ei luokiteltu Kiloview
- Ei luokiteltu Middle Atlantic
- Ei luokiteltu Mount-It!
- Ei luokiteltu Morley
- Ei luokiteltu Ampeg
- Ei luokiteltu Apantac
- Ei luokiteltu Carry-on
- Ei luokiteltu Liftmaster
- Ei luokiteltu GVision
- Ei luokiteltu IPGARD
- Ei luokiteltu Murideo
- Ei luokiteltu TK Audio
- Ei luokiteltu Rosco
- Ei luokiteltu Proaim
- Ei luokiteltu Cisco
- Ei luokiteltu CGV
- Ei luokiteltu Vacmaster
- Ei luokiteltu Elmo
- Ei luokiteltu Libec
- Ei luokiteltu Point Source Audio
- Ei luokiteltu Macally
- Ei luokiteltu Linhof
- Ei luokiteltu Ade
- Ei luokiteltu Di4
- Ei luokiteltu Mellerware
- Ei luokiteltu Zenec
- Ei luokiteltu Silver Cross
- Ei luokiteltu Allen & Heath
- Ei luokiteltu American DJ
- Ei luokiteltu AJA
- Ei luokiteltu EXO
- Ei luokiteltu RME
- Ei luokiteltu SurgeX
- Ei luokiteltu Alcon
- Ei luokiteltu Vantec
- Ei luokiteltu Silverline
- Ei luokiteltu VAVA
- Ei luokiteltu Tefal
- Ei luokiteltu Vicoustic
- Ei luokiteltu LERAN
- Ei luokiteltu Doffler
- Ei luokiteltu Novy
- Ei luokiteltu Profoto
- Ei luokiteltu TensCare
- Ei luokiteltu Scanstrut
- Ei luokiteltu Mad Dog
- Ei luokiteltu Industrial Music Electronics
- Ei luokiteltu Source Audio
- Ei luokiteltu Black Lion Audio
- Ei luokiteltu Wiha
- Ei luokiteltu Puls Dimension
- Ei luokiteltu Wasp
- Ei luokiteltu OSEE
- Ei luokiteltu Gamewright
- Ei luokiteltu ISDT
- Ei luokiteltu Ilve
- Ei luokiteltu Scosche
- Ei luokiteltu Reolink
- Ei luokiteltu Bebob
- Ei luokiteltu Ashly
- Ei luokiteltu Claypaky
- Ei luokiteltu Premier Mounts
- Ei luokiteltu MuxLab
- Ei luokiteltu Icy Box
- Ei luokiteltu Holosun
- Ei luokiteltu Seagate
- Ei luokiteltu Holzmann
- Ei luokiteltu Blackmagic Design
- Ei luokiteltu Audiolab
- Ei luokiteltu Lectrosonics
- Ei luokiteltu Gravity
- Ei luokiteltu Modbap Modular
- Ei luokiteltu Ikan
- Ei luokiteltu Genius
- Ei luokiteltu Silvercrest
- Ei luokiteltu Rommer
- Ei luokiteltu Traeger
- Ei luokiteltu Memphis Audio
- Ei luokiteltu Focal
- Ei luokiteltu Belkin
- Ei luokiteltu BDI
- Ei luokiteltu Alpine
- Ei luokiteltu Ring
- Ei luokiteltu TC Helicon
- Ei luokiteltu TomTom
- Ei luokiteltu XGIMI
- Ei luokiteltu Omron
- Ei luokiteltu Celestron
- Ei luokiteltu Gymform
- Ei luokiteltu Glide Gear
- Ei luokiteltu Oppo
- Ei luokiteltu Chicco
- Ei luokiteltu AVM
- Ei luokiteltu Impact
- Ei luokiteltu Pelco
- Ei luokiteltu FoxFury
- Ei luokiteltu Argoclima
- Ei luokiteltu Mammut
- Ei luokiteltu Huawei
- Ei luokiteltu Escort
- Ei luokiteltu Heritage Audio
- Ei luokiteltu Safco
- Ei luokiteltu Monoprice
- Ei luokiteltu Stabila
- Ei luokiteltu CTA Digital
- Ei luokiteltu Olight
- Ei luokiteltu Primo
- Ei luokiteltu HammerSmith
- Ei luokiteltu Cyrus
- Ei luokiteltu Steelbody
- Ei luokiteltu Ltech
- Ei luokiteltu Ventev
- Ei luokiteltu Elektrobock
- Ei luokiteltu Triton
- Ei luokiteltu Trisa
- Ei luokiteltu Corberó
- Ei luokiteltu AENO
- Ei luokiteltu Korg
- Ei luokiteltu Atosa
- Ei luokiteltu STANDIVARIUS
- Ei luokiteltu Avteq
- Ei luokiteltu Techly
- Ei luokiteltu Izzy
- Ei luokiteltu PureLink
- Ei luokiteltu BirdDog
- Ei luokiteltu UNYKAch
- Ei luokiteltu TeachLogic
- Ei luokiteltu Al-ko
- Ei luokiteltu ADATA
- Ei luokiteltu Mobotix
- Ei luokiteltu Kramer
- Ei luokiteltu ATen
- Ei luokiteltu Blustream
- Ei luokiteltu Laserworld
- Ei luokiteltu Genelec
- Ei luokiteltu Kunft
- Ei luokiteltu Milesight
- Ei luokiteltu Honda
- Ei luokiteltu Spanninga
- Ei luokiteltu Perel
- Ei luokiteltu Bialetti
- Ei luokiteltu Xlyne
- Ei luokiteltu Plant Craft
- Ei luokiteltu Sungrow
- Ei luokiteltu Grundfos
- Ei luokiteltu Bazooka
- Ei luokiteltu Carlsbro
- Ei luokiteltu MoFi
- Ei luokiteltu Blackburn
- Ei luokiteltu Mtx Audio
- Ei luokiteltu Bang And Olufsen
- Ei luokiteltu Delta Dore
- Ei luokiteltu Sole Fitness
- Ei luokiteltu Cowon
- Ei luokiteltu Theben
- Ei luokiteltu Grasslin
- Ei luokiteltu Orbis
- Ei luokiteltu Fantini Cosmi
- Ei luokiteltu Bebe Confort
- Ei luokiteltu WHALE
- Ei luokiteltu Stalco
- Ei luokiteltu Bunn
- Ei luokiteltu Horizon Fitness
- Ei luokiteltu Cobra
- Ei luokiteltu Sonel
- Ei luokiteltu Lamax
- Ei luokiteltu Jilong
- Ei luokiteltu Maytronics
- Ei luokiteltu Tempmate
- Ei luokiteltu Idec
- Ei luokiteltu Analog Way
- Ei luokiteltu Gamesir
- Ei luokiteltu ZyXEL
- Ei luokiteltu Vogue
- Ei luokiteltu Frilec
- Ei luokiteltu Yaesu
- Ei luokiteltu Concept2
- Ei luokiteltu Musical Fidelity
- Ei luokiteltu Flir
- Ei luokiteltu Rademacher
- Ei luokiteltu NGS
- Ei luokiteltu CTOUCH
- Ei luokiteltu Girmi
- Ei luokiteltu Auray
- Ei luokiteltu RCF
- Ei luokiteltu KJB Security Products
- Ei luokiteltu Harvia
- Ei luokiteltu Microchip
- Ei luokiteltu Homematic IP
- Ei luokiteltu Tektronix
- Ei luokiteltu WilTec
- Ei luokiteltu Easypix
- Ei luokiteltu LC-Power
- Ei luokiteltu SVS
- Ei luokiteltu 8BitDo
- Ei luokiteltu Pardini
- Ei luokiteltu Audeze
- Ei luokiteltu Be Quiet!
- Ei luokiteltu Ergobaby
- Ei luokiteltu Everdure
- Ei luokiteltu Tams Elektronik
- Ei luokiteltu Insta360
- Ei luokiteltu Fieldmann
- Ei luokiteltu Alpen Kreuzer
- Ei luokiteltu Xplora
- Ei luokiteltu H.Koenig
- Ei luokiteltu Wimberley
- Ei luokiteltu Playtive
- Ei luokiteltu Vimar
- Ei luokiteltu Osprey
- Ei luokiteltu Hosa
- Ei luokiteltu Havis
- Ei luokiteltu Pitsos
- Ei luokiteltu Lionelo
- Ei luokiteltu Physa
- Ei luokiteltu Steinberg
- Ei luokiteltu Daewoo
- Ei luokiteltu Emerson
- Ei luokiteltu Phoenix Gold
- Ei luokiteltu Aconatic
- Ei luokiteltu MBM
- Ei luokiteltu Oricom
- Ei luokiteltu Casablanca
- Ei luokiteltu Weasy
- Ei luokiteltu Biltema
- Ei luokiteltu Waves
- Ei luokiteltu Bogen
- Ei luokiteltu Electro Harmonix
- Ei luokiteltu Chrome-Q
- Ei luokiteltu Galaxy Audio
- Ei luokiteltu Altman
- Ei luokiteltu Aiphone
- Ei luokiteltu Atlas
- Ei luokiteltu Graco
- Ei luokiteltu MARTOR
- Ei luokiteltu Mean Well
- Ei luokiteltu Exelpet
- Ei luokiteltu Trendnet
- Ei luokiteltu G-Technology
- Ei luokiteltu CubuSynth
- Ei luokiteltu Simpson
- Ei luokiteltu Infasecure
- Ei luokiteltu SecureSafe
- Ei luokiteltu Intellinet
- Ei luokiteltu Hikoki
- Ei luokiteltu Emerio
- Ei luokiteltu Prime3
- Ei luokiteltu OBH Nordica
- Ei luokiteltu Butler
- Ei luokiteltu Duronic
- Ei luokiteltu AVer
- Ei luokiteltu IK Multimedia
- Ei luokiteltu Vankyo
- Ei luokiteltu Murr Elektronik
- Ei luokiteltu TDK-Lambda
- Ei luokiteltu Vitek
- Ei luokiteltu Texas
- Ei luokiteltu Reloop
- Ei luokiteltu ProfiCook
- Ei luokiteltu Arovec
- Ei luokiteltu Harman Kardon
- Ei luokiteltu ARRI
- Ei luokiteltu Yamazen
- Ei luokiteltu Lantus
- Ei luokiteltu Acti
- Ei luokiteltu GMB Gaming
- Ei luokiteltu Eurom
- Ei luokiteltu Cadac
- Ei luokiteltu Olympia
- Ei luokiteltu Osram
- Ei luokiteltu Patching Panda
- Ei luokiteltu Consul
- Ei luokiteltu Draytek
- Ei luokiteltu Manitowoc
- Ei luokiteltu Joranalogue
- Ei luokiteltu Klavis
- Ei luokiteltu HyperX
- Ei luokiteltu KDK
- Ei luokiteltu ChamSys
- Ei luokiteltu Creative
- Ei luokiteltu OneTouch
- Ei luokiteltu Kospel
- Ei luokiteltu Crosscall
- Ei luokiteltu Dynacord
- Ei luokiteltu Rapoo
- Ei luokiteltu Suunto
- Ei luokiteltu Roidmi
- Ei luokiteltu IOGEAR
- Ei luokiteltu Ferguson
- Ei luokiteltu Adventuridge
- Ei luokiteltu Artecta
- Ei luokiteltu WyreStorm
- Ei luokiteltu IBEAM
- Ei luokiteltu ToughTested
- Ei luokiteltu Mattel
- Ei luokiteltu Baby Jogger
- Ei luokiteltu Savio
- Ei luokiteltu Healthy Choice
- Ei luokiteltu Yato
- Ei luokiteltu Lund
- Ei luokiteltu Oromed
- Ei luokiteltu Acefast
- Ei luokiteltu Porter-Cable
- Ei luokiteltu Christmas Time
- Ei luokiteltu Barazza
- Ei luokiteltu Chacon
- Ei luokiteltu Marmitek
- Ei luokiteltu Nivona
- Ei luokiteltu Thermador
- Ei luokiteltu Dehner
- Ei luokiteltu Eliminator Lighting
- Ei luokiteltu Microboards
- Ei luokiteltu Kopul
- Ei luokiteltu JoeCo
- Ei luokiteltu BZBGear
- Ei luokiteltu Fiilex
- Ei luokiteltu Gen Energy
- Ei luokiteltu DEERSYNC
- Ei luokiteltu ChyTV
- Ei luokiteltu Bresser
- Ei luokiteltu Arkon
- Ei luokiteltu Apollo Design
- Ei luokiteltu Ardes
- Ei luokiteltu Tesseract Modular
- Ei luokiteltu Zanussi
- Ei luokiteltu Bulgin
- Ei luokiteltu Foscam
- Ei luokiteltu AV:link
- Ei luokiteltu Pure 100
- Ei luokiteltu Hirschmann
- Ei luokiteltu Clatronic
- Ei luokiteltu Interphone
- Ei luokiteltu Kernau
- Ei luokiteltu Babybjörn
- Ei luokiteltu Hanseatic
- Ei luokiteltu Proline
- Ei luokiteltu Xblitz
- Ei luokiteltu Hager
- Ei luokiteltu Hecht
- Ei luokiteltu Konica Minolta
- Ei luokiteltu Neumann
- Ei luokiteltu Kathrein
- Ei luokiteltu STANDARD
- Ei luokiteltu BigBlue
- Ei luokiteltu RC Allen
- Ei luokiteltu Plastkon
- Ei luokiteltu Neutrik
- Ei luokiteltu Aquasure
- Ei luokiteltu Beautiful
- Ei luokiteltu Triplett
- Ei luokiteltu Alfatron
- Ei luokiteltu Bowflex
- Ei luokiteltu Kino Flo
- Ei luokiteltu SmallRig
- Ei luokiteltu Cateye
- Ei luokiteltu Genie
- Ei luokiteltu GVM
- Ei luokiteltu Soler & Palau
- Ei luokiteltu Thule
- Ei luokiteltu Burg-Wachter
- Ei luokiteltu Stelton
- Ei luokiteltu Bavaria
- Ei luokiteltu Medela
- Ei luokiteltu AVerMedia
- Ei luokiteltu Logitech
- Ei luokiteltu Beemoo
- Ei luokiteltu Chandler
- Ei luokiteltu Hotone
- Ei luokiteltu Klark Teknik
- Ei luokiteltu Auer Signal
- Ei luokiteltu Shimbol
- Ei luokiteltu Hedbox
- Ei luokiteltu Flycam
- Ei luokiteltu Tele Vue
- Ei luokiteltu Atdec
- Ei luokiteltu Honey-Can-Do
- Ei luokiteltu Think Tank
- Ei luokiteltu Princeton Tec
- Ei luokiteltu Phonic
- Ei luokiteltu Ultimate Support
- Ei luokiteltu Minox
- Ei luokiteltu Maxxmee
- Ei luokiteltu Propellerhead
- Ei luokiteltu Nilfisk
- Ei luokiteltu Crosley
- Ei luokiteltu Wiesenfield
- Ei luokiteltu Sun Joe
- Ei luokiteltu Blomberg
- Ei luokiteltu Fellowes
- Ei luokiteltu Ferplast
- Ei luokiteltu Bushnell
- Ei luokiteltu Parkside
- Ei luokiteltu Cardo
- Ei luokiteltu Cooler Master
- Ei luokiteltu Olympus
- Ei luokiteltu Black Decker
- Ei luokiteltu ART
- Ei luokiteltu Toolland
- Ei luokiteltu Zipper
- Ei luokiteltu Inkbird
- Ei luokiteltu Continental Edison
- Ei luokiteltu NUX
- Ei luokiteltu Gabor
- Ei luokiteltu Cleanmaxx
- Ei luokiteltu Sôlt
- Ei luokiteltu EGO
- Ei luokiteltu Rollei
- Ei luokiteltu Bugaboo
- Ei luokiteltu Zhiyun
- Ei luokiteltu Koenig
- Ei luokiteltu Angler
- Ei luokiteltu Testboy
- Ei luokiteltu Baby Lock
- Ei luokiteltu Devialet
- Ei luokiteltu Hozelock
- Ei luokiteltu Sime
- Ei luokiteltu NovaStar
- Ei luokiteltu Petite Chérie
- Ei luokiteltu Taga Harmony
- Ei luokiteltu DPM
- Ei luokiteltu Strong
- Ei luokiteltu ACCU-CHEK
- Ei luokiteltu SoundTube
- Ei luokiteltu Njoy
- Ei luokiteltu Leica
- Ei luokiteltu Studio Titan
- Ei luokiteltu EOTech
- Ei luokiteltu AstrHori
- Ei luokiteltu Icron
- Ei luokiteltu Pyrex
- Ei luokiteltu Marklin
- Ei luokiteltu MJX
- Ei luokiteltu RTS
- Ei luokiteltu Ebro
- Ei luokiteltu James
- Ei luokiteltu Visage
- Ei luokiteltu Geemarc
- Ei luokiteltu Ruark Audio
- Ei luokiteltu Platypus
- Ei luokiteltu DEHN
- Ei luokiteltu Panamax
- Ei luokiteltu Trezor
- Ei luokiteltu Raya
- Ei luokiteltu EtherWAN
- Ei luokiteltu ClearOne
- Ei luokiteltu Aqua-Vu
- Ei luokiteltu Ferrofish
- Ei luokiteltu HPRC
- Ei luokiteltu Dracast
- Ei luokiteltu Really Right Stuff
- Ei luokiteltu Decimator
- Ei luokiteltu ColorKey
- Ei luokiteltu Key Digital
- Ei luokiteltu Chimera
- Ei luokiteltu Eartec
- Ei luokiteltu ButtKicker
- Ei luokiteltu Gra-Vue
- Ei luokiteltu Pliant Technologies
- Ei luokiteltu Blonder Tongue
- Ei luokiteltu ZWO
- Ei luokiteltu Ocean Matrix
- Ei luokiteltu MEPROLIGHT
- Ei luokiteltu Antelope
- Ei luokiteltu Crystal Video
- Ei luokiteltu Vixen
- Ei luokiteltu Magnus
- Ei luokiteltu Senal
- Ei luokiteltu Avenview
- Ei luokiteltu Digigram
- Ei luokiteltu Tilta
- Ei luokiteltu Futaba
- Ei luokiteltu AVMATRIX
- Ei luokiteltu Luxli
- Ei luokiteltu Hawk-Woods
- Ei luokiteltu SWIT
- Ei luokiteltu PAG
- Ei luokiteltu Simeo
- Ei luokiteltu Walrus Audio
- Ei luokiteltu CEDAR
- Ei luokiteltu Lenco
- Ei luokiteltu Wachendorff
- Ei luokiteltu Senseca
- Ei luokiteltu NeoMounts
- Ei luokiteltu Western Co.
- Ei luokiteltu WEG
- Ei luokiteltu ProFlo
- Ei luokiteltu Rohl
- Ei luokiteltu Vivolink
- Ei luokiteltu Protector
- Ei luokiteltu Allibert
- Ei luokiteltu IDIS
- Ei luokiteltu Victrola
- Ei luokiteltu Godrej
- Ei luokiteltu Gardenline
- Ei luokiteltu Intel
- Ei luokiteltu Mooer
- Ei luokiteltu M-Audio
- Ei luokiteltu Astralpool
- Ei luokiteltu Oregon Scientific
- Ei luokiteltu Robus
- Ei luokiteltu SureFire
- Ei luokiteltu Nebula
- Ei luokiteltu Core SWX
- Ei luokiteltu KeepOut
- Ei luokiteltu Dexibell
- Ei luokiteltu Dali
- Ei luokiteltu EQ-3
- Ei luokiteltu Akai
- Ei luokiteltu Metronic
- Ei luokiteltu COLBOR
- Ei luokiteltu Berker
- Ei luokiteltu Tornado
- Ei luokiteltu Hollyland
- Ei luokiteltu Moman
- Ei luokiteltu DiversiTech
- Ei luokiteltu Aukey
- Ei luokiteltu ICE Watch
- Ei luokiteltu Violectric
- Ei luokiteltu Aalberg Audio
- Ei luokiteltu Steelseries
- Ei luokiteltu LAS
- Ei luokiteltu Bolt
- Ei luokiteltu Xcellon
- Ei luokiteltu Ruggard
- Ei luokiteltu Elvid
- Ei luokiteltu OM SYSTEM
- Ei luokiteltu OKAY
- Ei luokiteltu OpenVox
- Ei luokiteltu POLARIS
- Ei luokiteltu 4ms
- Ei luokiteltu Hobart
- Ei luokiteltu JAYS
- Ei luokiteltu Sogo
- Ei luokiteltu Kolcraft
- Ei luokiteltu SKROSS
- Ei luokiteltu Total Chef
- Ei luokiteltu Tascam
- Ei luokiteltu Evooch
- Ei luokiteltu Pontec
- Ei luokiteltu Trace Elliot
- Ei luokiteltu Klauke
- Ei luokiteltu Tiger
- Ei luokiteltu AOpen
- Ei luokiteltu Lazer
- Ei luokiteltu Symmons
- Ei luokiteltu DMT
- Ei luokiteltu Golden Age Project
- Ei luokiteltu Ambrogio
- Ei luokiteltu Umidigi
- Ei luokiteltu Bolin Technology
- Ei luokiteltu Warmup
- Ei luokiteltu Rexing
- Ei luokiteltu Aduro
- Ei luokiteltu Williams Sound
- Ei luokiteltu Newline
- Ei luokiteltu Total
- Ei luokiteltu HK Audio
- Ei luokiteltu PoLabs
- Ei luokiteltu Astell&Kern
- Ei luokiteltu Taiji
- Ei luokiteltu Futurelight
- Ei luokiteltu Jacuzzi
- Ei luokiteltu Gioteck
- Ei luokiteltu Gerber
- Ei luokiteltu Royale
- Ei luokiteltu Z CAM
- Ei luokiteltu Pentatech
- Ei luokiteltu Studiologic
- Ei luokiteltu Hammond
- Ei luokiteltu Ketron
- Ei luokiteltu MGL Avionics
- Ei luokiteltu Digi-Pas
- Ei luokiteltu Marshall Electronics
- Ei luokiteltu Grace Design
- Ei luokiteltu Grimm Audio
- Ei luokiteltu Lucide
- Ei luokiteltu Urbanista
- Ei luokiteltu Cherry
- Ei luokiteltu Pfister
- Ei luokiteltu InfiRay
- Ei luokiteltu Arduino
- Ei luokiteltu JANDY
- Ei luokiteltu Fellow
- Ei luokiteltu Peerless-AV
- Ei luokiteltu Engel
- Ei luokiteltu Elbe
- Ei luokiteltu GolfBuddy
- Ei luokiteltu Lotus
- Ei luokiteltu Equator
- Ei luokiteltu Eura
- Ei luokiteltu Axler
- Ei luokiteltu Das Keyboard
- Ei luokiteltu Schaffner
- Ei luokiteltu Vitec
- Ei luokiteltu Technaxx
- Ei luokiteltu Velbus
- Ei luokiteltu Nicols
- Ei luokiteltu Jane
- Ei luokiteltu Adder
- Ei luokiteltu DAP Audio
- Ei luokiteltu Singer
- Ei luokiteltu Dubatti
- Ei luokiteltu Venicci
- Ei luokiteltu Baby Trend
- Ei luokiteltu Watson
- Ei luokiteltu Sabrent
- Ei luokiteltu Inglesina
- Ei luokiteltu Ernitec
- Ei luokiteltu Fito
- Ei luokiteltu Matterport
- Ei luokiteltu Comprehensive
- Ei luokiteltu Legamaster
- Ei luokiteltu Deaf Bonce
- Ei luokiteltu Vogels
- Ei luokiteltu AZZA
- Ei luokiteltu Onkyo
- Ei luokiteltu Mercusys
- Ei luokiteltu Defender
- Ei luokiteltu Hamlet
- Ei luokiteltu Revlon
- Ei luokiteltu Wallas
- Ei luokiteltu ARNOLD Lichttechnik
- Ei luokiteltu Sescom
- Ei luokiteltu API Audio
- Ei luokiteltu Atlantis Land
- Ei luokiteltu Bestway
- Ei luokiteltu Moomin
- Ei luokiteltu Belulu
- Ei luokiteltu YSI
- Ei luokiteltu Jedo
- Ei luokiteltu RIX
- Ei luokiteltu Bayco
- Ei luokiteltu Wilson
- Ei luokiteltu Ionmax
- Ei luokiteltu Creality
- Ei luokiteltu Compex
- Ei luokiteltu Crelando
- Ei luokiteltu Algo
- Ei luokiteltu Dinstar
- Ei luokiteltu FeiyuTech
- Ei luokiteltu EMeet
- Ei luokiteltu Ergotools Pattfield
- Ei luokiteltu Motrona
- Ei luokiteltu NordicTrack
- Ei luokiteltu CaterRacks
- Ei luokiteltu Flama
- Ei luokiteltu Sedona
- Ei luokiteltu Uniross
- Ei luokiteltu Akasa
- Ei luokiteltu Perixx
- Ei luokiteltu Noordi
- Ei luokiteltu Globalo
- Ei luokiteltu SwitchBot
- Ei luokiteltu Corona
- Ei luokiteltu Michelin
- Ei luokiteltu Adonit
- Ei luokiteltu Bavaria By Einhell
- Ei luokiteltu Schwinn
- Ei luokiteltu Antec
- Ei luokiteltu Nuki
- Ei luokiteltu SoundPEATS
- Ei luokiteltu MagnaPool
- Ei luokiteltu Sensiplast
- Ei luokiteltu OWC
- Ei luokiteltu Krone
- Ei luokiteltu Coors Light
- Ei luokiteltu Konig & Meyer
- Ei luokiteltu Telestar
- Ei luokiteltu Arco
- Ei luokiteltu Brita
- Ei luokiteltu Aguilar
- Ei luokiteltu Exibel
- Ei luokiteltu GPX
- Ei luokiteltu KoolScapes
- Ei luokiteltu GFM
- Ei luokiteltu Ideal
- Ei luokiteltu Avid
- Ei luokiteltu On-Q
- Ei luokiteltu Synco
- Ei luokiteltu HQ Power
- Ei luokiteltu Jonard Tools
- Ei luokiteltu Adesso
- Ei luokiteltu Royal Sovereign
- Ei luokiteltu Beurer
- Ei luokiteltu Kubo
- Ei luokiteltu Netter Vibration
- Ei luokiteltu Govee
- Ei luokiteltu Califone
- Ei luokiteltu Sunding
- Ei luokiteltu Teesa
- Ei luokiteltu Bliss Outdoors
- Ei luokiteltu BeSafe
- Ei luokiteltu Martin Logan
- Ei luokiteltu Air Guard
- Ei luokiteltu Oase
- Ei luokiteltu Livington
- Ei luokiteltu Phoenix Contact
- Ei luokiteltu Lanaform
- Ei luokiteltu Elcom
- Ei luokiteltu DEXP
- Ei luokiteltu Platinum
- Ei luokiteltu Scala
- Ei luokiteltu Petkit
- Ei luokiteltu Geuther
- Ei luokiteltu Rainbow
- Ei luokiteltu Kress
- Ei luokiteltu Emko
- Ei luokiteltu Lenoxx
- Ei luokiteltu Westfalia
- Ei luokiteltu Martin Audio
- Ei luokiteltu Gloria
- Ei luokiteltu Hurricane
- Ei luokiteltu Tiptop Audio
- Ei luokiteltu Winix
- Ei luokiteltu Blanco
- Ei luokiteltu GoPro
- Ei luokiteltu Interstuhl
- Ei luokiteltu Powerfix
- Ei luokiteltu Babyzen
- Ei luokiteltu Aqua Joe
- Ei luokiteltu Fiio
- Ei luokiteltu Nokia
- Ei luokiteltu Mackie
- Ei luokiteltu Astro
- Ei luokiteltu Carel
- Ei luokiteltu Medisana
- Ei luokiteltu Line 6
- Ei luokiteltu Parallels
- Ei luokiteltu Arturia
- Ei luokiteltu Dynon Avionics
- Ei luokiteltu Uvex
- Ei luokiteltu Florabest
- Ei luokiteltu Crivit
- Ei luokiteltu Creality3D
- Ei luokiteltu Beaba
- Ei luokiteltu Tork
- Ei luokiteltu DBX
- Ei luokiteltu Lescha
- Ei luokiteltu Grunkel
- Ei luokiteltu Babymoov
- Ei luokiteltu Lezyne
- Ei luokiteltu Fibaro
- Ei luokiteltu Vitalmaxx
- Ei luokiteltu Swissvoice
- Ei luokiteltu Intex
- Ei luokiteltu Joie
- Ei luokiteltu Proficare
- Ei luokiteltu Redrock Micro
- Ei luokiteltu Vortex
- Ei luokiteltu Sekonic
- Ei luokiteltu HiFi ROSE
- Ei luokiteltu UAvionix
- Ei luokiteltu Audibax
- Ei luokiteltu GW Instek
- Ei luokiteltu Evenflo
- Ei luokiteltu Ledger
- Ei luokiteltu LARQ
- Ei luokiteltu Auriol
- Ei luokiteltu Luxman
- Ei luokiteltu Rittal
- Ei luokiteltu InSinkErator
- Ei luokiteltu ORCA
- Ei luokiteltu SSV Works
- Ei luokiteltu Eminent
- Ei luokiteltu PreSonus
- Ei luokiteltu Basil
- Ei luokiteltu Swift
- Ei luokiteltu TOTO
- Ei luokiteltu Sonos
- Ei luokiteltu Brilliant
- Ei luokiteltu AEA
- Ei luokiteltu AcuRite
- Ei luokiteltu Chamberlain
- Ei luokiteltu YA-MAN
- Ei luokiteltu Doro
- Ei luokiteltu Sonicware
- Ei luokiteltu CRAFT + MAIN
- Ei luokiteltu Roline
- Ei luokiteltu Carrier
- Ei luokiteltu V-Tone
- Ei luokiteltu Hellberg
- Ei luokiteltu HELGI
- Ei luokiteltu Gold Note
- Ei luokiteltu Dual
- Ei luokiteltu Redsbaby
- Ei luokiteltu Hovicon
- Ei luokiteltu Bryton
- Ei luokiteltu Western Digital
- Ei luokiteltu Seaward
- Ei luokiteltu Rockford Fosgate
- Ei luokiteltu Parasound
- Ei luokiteltu Stelzner
- Ei luokiteltu LightKeeper Pro
- Ei luokiteltu JennAir
- Ei luokiteltu Esatto
- Ei luokiteltu Cressi
- Ei luokiteltu DoorBird
- Ei luokiteltu Hacienda
- Ei luokiteltu Singercon
- Ei luokiteltu Dymo
- Ei luokiteltu Magivaac
- Ei luokiteltu Gem Toys
- Ei luokiteltu Intergas
- Ei luokiteltu Budda
- Ei luokiteltu Muller
- Ei luokiteltu Paladin
- Ei luokiteltu Pivo
- Ei luokiteltu Amazfit
- Ei luokiteltu Sharkbite
- Ei luokiteltu XPG
- Ei luokiteltu BMAX
- Ei luokiteltu Camille Bauer
- Ei luokiteltu Meopta
- Ei luokiteltu KanexPro
- Ei luokiteltu Cranborne Audio
- Ei luokiteltu InLine
- Ei luokiteltu Tactical Fiber Systems
- Ei luokiteltu Telmax
- Ei luokiteltu Sonifex
- Ei luokiteltu ARC
- Ei luokiteltu Magnavox
- Ei luokiteltu Zodiac
- Ei luokiteltu Starlyf
- Ei luokiteltu President
- Ei luokiteltu Galcon
- Ei luokiteltu K&M
- Ei luokiteltu CatSynth
- Ei luokiteltu (Recovery)
- Ei luokiteltu Crucial
- Ei luokiteltu Echo
- Ei luokiteltu Trijicon
- Ei luokiteltu Vertex
- Ei luokiteltu PTZ Optics
- Ei luokiteltu Revic
- Ei luokiteltu Kahayan
- Ei luokiteltu Nureva
- Ei luokiteltu Pawa
- Ei luokiteltu Stamina
- Ei luokiteltu Lemair
- Ei luokiteltu Soundsphere
- Ei luokiteltu BSS Audio
- Ei luokiteltu Simplified MFG
- Ei luokiteltu Eero
- Ei luokiteltu Springfree
- Ei luokiteltu Titanwolf
- Ei luokiteltu Perfect Christmas
- Ei luokiteltu Medicinalis
- Ei luokiteltu Uplink
- Ei luokiteltu Rupert Neve Designs
- Ei luokiteltu Thorens
- Ei luokiteltu Microair
- Ei luokiteltu XCell
- Ei luokiteltu Tepro
- Ei luokiteltu Traco Power
- Ei luokiteltu Yellow Garden Line
- Ei luokiteltu Microsoft
- Ei luokiteltu Liam&Daan
- Ei luokiteltu Primewire
- Ei luokiteltu Snow Joe
- Ei luokiteltu Universal Audio
- Ei luokiteltu Soundmaster
- Ei luokiteltu Casa Deco
- Ei luokiteltu Nutrichef
- Ei luokiteltu Inverx
- Ei luokiteltu Ugreen
- Ei luokiteltu Haeger
- Ei luokiteltu Google
- Ei luokiteltu EAT
- Ei luokiteltu Vincent
- Ei luokiteltu Jinbei
- Ei luokiteltu Sound Devices
- Ei luokiteltu Geneva
- Ei luokiteltu Indiana Line
- Ei luokiteltu Graphite
- Ei luokiteltu Sumiko
- Ei luokiteltu On-Stage
- Ei luokiteltu Ambient Weather
- Ei luokiteltu Anybus
- Ei luokiteltu Enhance
- Ei luokiteltu BASSBOSS
- Ei luokiteltu Digitalinx
- Ei luokiteltu Easyrig
- Ei luokiteltu Ocean Way Audio
- Ei luokiteltu Dobot
- Ei luokiteltu MAK
- Ei luokiteltu Easymaxx
- Ei luokiteltu Christmaxx
- Ei luokiteltu Multibrackets
- Ei luokiteltu Exagerate
- Ei luokiteltu Clarion
- Ei luokiteltu Cricut
- Ei luokiteltu Ember
- Ei luokiteltu Sifflus
- Ei luokiteltu ADDAC System
- Ei luokiteltu FBT
- Ei luokiteltu Primera
- Ei luokiteltu Hecate
- Ei luokiteltu Alutruss
- Ei luokiteltu LightZone
- Ei luokiteltu Nacon
- Ei luokiteltu Peak Design
- Ei luokiteltu AVPro Edge
- Ei luokiteltu Blizzard
- Ei luokiteltu Drawmer
- Ei luokiteltu ACOPower
- Ei luokiteltu AGM
- Ei luokiteltu Hanwha
- Ei luokiteltu Edelkrone
- Ei luokiteltu Transparent
- Ei luokiteltu ESE
- Ei luokiteltu Uniropa
- Ei luokiteltu IHome
- Ei luokiteltu JMAZ Lighting
- Ei luokiteltu GeoVision
- Ei luokiteltu NightStick
- Ei luokiteltu JK Audio
- Ei luokiteltu MIOPS
- Ei luokiteltu Hawke
- Ei luokiteltu Rotatrim
- Ei luokiteltu Enttec
- Ei luokiteltu Robinhood
- Ei luokiteltu Feelworld
- Ei luokiteltu Eller
- Ei luokiteltu Arthur Martin
- Ei luokiteltu Soundcraft
- Ei luokiteltu Andover
- Ei luokiteltu Fortinet
- Ei luokiteltu Prestigio
- Ei luokiteltu Deity
- Ei luokiteltu CMI
- Ei luokiteltu Betty Bossi
- Ei luokiteltu CAD Audio
- Ei luokiteltu Moulinex
- Ei luokiteltu Merging
- Ei luokiteltu AirTurn
- Ei luokiteltu Altrad
- Ei luokiteltu New Pol
- Ei luokiteltu Expressive E
- Ei luokiteltu ILive
- Ei luokiteltu Giardino
- Ei luokiteltu Mutec
- Ei luokiteltu Ipevo
- Ei luokiteltu Mafell
- Ei luokiteltu Autel
- Ei luokiteltu Crane
- Ei luokiteltu DOD
- Ei luokiteltu Videotel Digital
- Ei luokiteltu Burris
- Ei luokiteltu FSR
- Ei luokiteltu PulseAudio
- Ei luokiteltu Black Box
- Ei luokiteltu Infantino
- Ei luokiteltu Bestgreen
- Ei luokiteltu Empress Effects
- Ei luokiteltu Enbrighten
- Ei luokiteltu Audison
- Ei luokiteltu Flame
- Ei luokiteltu Garden Feelings
- Ei luokiteltu UDG Gear
- Ei luokiteltu Lastolite
- Ei luokiteltu Weidmüller
- Ei luokiteltu NANO Modules
- Ei luokiteltu EA Elektro Automatik
- Ei luokiteltu Bahr
- Ei luokiteltu Grand Effects
- Ei luokiteltu Franklin
- Ei luokiteltu Sodapop
- Ei luokiteltu Absco
- Ei luokiteltu Victor Technology
- Ei luokiteltu Lowepro
- Ei luokiteltu Celexon
- Ei luokiteltu Neumärker
- Ei luokiteltu SunPower
- Ei luokiteltu Black Line
- Ei luokiteltu RCBS
- Ei luokiteltu Hensel
- Ei luokiteltu Ultimate
- Ei luokiteltu Westland
- Ei luokiteltu For_Q
- Ei luokiteltu Pro-User
- Ei luokiteltu Flavel
- Ei luokiteltu Deltaco Gaming
- Ei luokiteltu Bluebird
- Ei luokiteltu Dunlop
- Ei luokiteltu Cotek
- Ei luokiteltu Deditec
- Ei luokiteltu Firefield
- Ei luokiteltu Cosi Home
- Ei luokiteltu Red Digital Cinema
- Ei luokiteltu Qian
- Ei luokiteltu JLCooper
- Ei luokiteltu Pelican
- Ei luokiteltu Nubert
- Ei luokiteltu Ixxat
- Ei luokiteltu GeoBox
- Ei luokiteltu URC
- Ei luokiteltu Advanced Network Devices
- Ei luokiteltu Broil King
- Ei luokiteltu Telycam
- Ei luokiteltu SafeMi
- Ei luokiteltu Aim TTi
- Ei luokiteltu GC Audio
- Ei luokiteltu GOgroove
- Ei luokiteltu XTRARM
- Ei luokiteltu Rock N Roller
- Ei luokiteltu Lynx
- Ei luokiteltu DQ
- Ei luokiteltu Nextorage
- Ei luokiteltu Varta
- Ei luokiteltu 2hp
- Ei luokiteltu Strymon
- Ei luokiteltu Morphor
- Ei luokiteltu Buchla & TipTop Audio
- Ei luokiteltu Twisted Electrons
- Ei luokiteltu OptiTrack
- Ei luokiteltu ZZ-2
- Ei luokiteltu E-ast
- Ei luokiteltu BMW
- Ei luokiteltu Datapath
- Ei luokiteltu Gima
- Ei luokiteltu Doona
- Ei luokiteltu Soundskins
- Ei luokiteltu Trio Lighting
- Ei luokiteltu Emga
- Ei luokiteltu SolidDrive
- Ei luokiteltu Induction Dynamics
- Ei luokiteltu USL
- Ei luokiteltu Chord
- Ei luokiteltu SKB
- Ei luokiteltu Paradigm
- Ei luokiteltu Vermeiren
- Ei luokiteltu Cyber Acoustics
- Ei luokiteltu Sangean
- Ei luokiteltu Freewell
- Ei luokiteltu Vivotek
- Ei luokiteltu ESI
- Ei luokiteltu Bright Starts
- Ei luokiteltu Troy-Bilt
- Ei luokiteltu Desview
- Ei luokiteltu Audio Pro
- Ei luokiteltu Foppapedretti
- Ei luokiteltu Drive Medical
- Ei luokiteltu Brändi
- Ei luokiteltu QZ
- Ei luokiteltu MSolutions
- Ei luokiteltu IPEGA
- Ei luokiteltu Marathon
- Ei luokiteltu ENDORFY
- Ei luokiteltu Matrox
- Ei luokiteltu Evolis
- Ei luokiteltu Sissel
- Ei luokiteltu PUR
- Ei luokiteltu Helight
- Ei luokiteltu Longvie
- Ei luokiteltu Act
- Ei luokiteltu Xuma
- Ei luokiteltu Ledvance
- Ei luokiteltu Magewell
- Ei luokiteltu Go-eCharger
- Ei luokiteltu GLP
- Ei luokiteltu DARTS
- Ei luokiteltu ETON
- Ei luokiteltu Singularity Computers
- Ei luokiteltu Boehringer Ingelheim
- Ei luokiteltu Sonorous
- Ei luokiteltu Iluv
- Ei luokiteltu Unitech
- Ei luokiteltu Sesame Street
- Ei luokiteltu Ingenuity
- Ei luokiteltu Lava
- Ei luokiteltu Digital Forecast
- Ei luokiteltu Autoscript
- Ei luokiteltu Artrom
- Ei luokiteltu Pigtronix
- Ei luokiteltu Mac Tools
- Ei luokiteltu Goal Zero
- Ei luokiteltu Icon
- Ei luokiteltu InvisibleShield
- Ei luokiteltu Voigtlander
- Ei luokiteltu Nuance
- Ei luokiteltu Bush
- Ei luokiteltu SLV
- Ei luokiteltu Hailo
- Ei luokiteltu Nyko
- Ei luokiteltu XD-Design
- Ei luokiteltu Step2
- Ei luokiteltu Gator
- Ei luokiteltu SmartGyro
- Ei luokiteltu Megableu
- Ei luokiteltu Needit
- Ei luokiteltu Brabantia
- Ei luokiteltu Dreamland
- Ei luokiteltu Star Belly
- Ei luokiteltu Pabobo
- Ei luokiteltu Stiebel Eltron
- Ei luokiteltu Tiny Love
- Ei luokiteltu Targus
- Ei luokiteltu BioChef
- Ei luokiteltu Cubot
- Ei luokiteltu Nevadent
- Ei luokiteltu IMG Stageline
- Ei luokiteltu Oras
- Ei luokiteltu SetonixSynth
- Ei luokiteltu Qu-Bit
- Ei luokiteltu Ergotron
- Ei luokiteltu Phase Technology
- Ei luokiteltu Casr
- Ei luokiteltu Hypnos
- Ei luokiteltu CkeyiN
- Ei luokiteltu Pulsar
- Ei luokiteltu BlaknBlu
- Ei luokiteltu Louroe Electronics
- Ei luokiteltu Leifheit
- Ei luokiteltu Orbitrek
- Ei luokiteltu Zaahn
- Ei luokiteltu Fischer
- Ei luokiteltu Livn
- Ei luokiteltu Kaorka
- Ei luokiteltu Brinno
- Ei luokiteltu MOOOV
- Ei luokiteltu DB Technologies
- Ei luokiteltu Expobar
- Ei luokiteltu Crem
- Ei luokiteltu Tece
- Ei luokiteltu CLIMAQUA
- Ei luokiteltu Airlive
- Ei luokiteltu Sportime
- Ei luokiteltu Wise
- Ei luokiteltu Quasar Science
- Ei luokiteltu Zeapon
- Ei luokiteltu Beltronics
- Ei luokiteltu Keter
- Ei luokiteltu Sommer
- Ei luokiteltu VOREL
- Ei luokiteltu Noise Engineering
- Ei luokiteltu UGo
- Ei luokiteltu Lahti Pro
- Ei luokiteltu Nous
- Ei luokiteltu Koliber
- Ei luokiteltu Jan Nowak
- Ei luokiteltu HiRO
- Ei luokiteltu Vantrue
- Ei luokiteltu Elight
- Ei luokiteltu Forodi
- Ei luokiteltu CELLFAST
- Ei luokiteltu MOZOS
- Ei luokiteltu RAM Mounts
- Ei luokiteltu Buxton
- Ei luokiteltu Adobe
- Ei luokiteltu Toorx
- Ei luokiteltu ViewZ
- Ei luokiteltu IsoTek
- Ei luokiteltu Miracle Smile
- Ei luokiteltu Zacuto
- Ei luokiteltu VARI-LITE
- Ei luokiteltu Real Cable
- Ei luokiteltu Syrp
- Ei luokiteltu Playseat
- Ei luokiteltu Satco
- Ei luokiteltu Evga
- Ei luokiteltu Racktime
- Ei luokiteltu Videotec
- Ei luokiteltu Pengo
- Ei luokiteltu FABER CASTELL
- Ei luokiteltu Agfa
- Ei luokiteltu Sloan
- Ei luokiteltu Sophos
- Ei luokiteltu Kica
- Ei luokiteltu Moxa
- Ei luokiteltu Sunny
- Ei luokiteltu Lowel
- Ei luokiteltu Leba
- Ei luokiteltu Kendall Howard
- Ei luokiteltu Starlight Xpress
- Ei luokiteltu Humminbird
- Ei luokiteltu Digitech
- Ei luokiteltu PAX
- Ei luokiteltu Sightron
- Ei luokiteltu Simmons
- Ei luokiteltu Woood
- Ei luokiteltu Infosec
- Ei luokiteltu Guide
- Ei luokiteltu Therm-a-Rest
- Ei luokiteltu Hoffman
- Ei luokiteltu Elbro
- Ei luokiteltu Vulcan
- Ei luokiteltu Diamond Audio
- Ei luokiteltu Nofred
- Ei luokiteltu Newport Brass
- Ei luokiteltu Ambient
- Ei luokiteltu AudioQuest
Viimeisimmät Ei luokiteltu Käyttöohjeet

9 Huhtikuuta 2025

9 Huhtikuuta 2025

9 Huhtikuuta 2025

9 Huhtikuuta 2025

9 Huhtikuuta 2025

9 Huhtikuuta 2025

9 Huhtikuuta 2025

9 Huhtikuuta 2025

9 Huhtikuuta 2025

9 Huhtikuuta 2025